Imagine the intricate dance between a plane’s wings and the air around them. To truly grasp this relationship, we need to dive into dynamic aeroelasticity, and that’s exactly what Nastran Solution 146 Monpnt1 RMS helps us do.
Table of Contents
Introduction to Dynamic Aeroelasticity and Nastran Solution
Dynamic aeroelasticity is an important area of study in engineering that studies the time-varying effects of aerodynamic force and structural deformation. It is very widely used in different fields, such as aerospace and mechanical structures. When the structures undergo an exchange of fluid flow, their behaviour changes significantly and results in complex responses that require further examination. Knowledge of these interactions is critical to the safety and performance of aircraft and their systems and subsystems.
To solve such problems more specifically and more effectively, Nastran, an advanced computational software common in aerospace engineering, helps engineers. Out of them, Nastran Solution 146 Monpnt1 RMS specializes in dynamic aeroelasticity matrix computation. This particular solution offers an affirmative approach to the assessment of dynamic aerodynamic loading on structures. Specifically, elements of fluid dynamics and structural mechanics integrated into Nastran allow for simplifying the flow of decision-making in terms of design optimizations, potential behaviours, and risks related to aerodynamic loads.

Understanding the Monpnt1 RMS Approach
Innovative Methodology for RMS Evaluation
As practised within the Nastran Solution 146 Monpnt1 RMS frameworks, the Monpnt1 RMS approach offers a breakthrough in the assessment of dynamic aeroelasticity. This methodology is expected to enable the determination of RMS values of the structural responses that can be used to assess the performance of dynamically loaded aeroelastic systems. Monpnt1 as a model is based on linear dynamics where aerodynamic forces and structural displacements are contributed as inputs to the model and they are analyzed for their interactions.
Modal Analysis Insights
The Monpnt1 RMS technique is based on the use of response statistics and modal analysis as primary parameters. It applies the eigenvalue extraction process to derive the natural frequencies and mode shapes of a structure because the knowledge of the modal characteristics is crucial when responding to dynamic loads. This modal information is then combined with aerodynamic information to predict the overall behaviour of the total system. The assumption that the problem is linear means that its mathematical representation is simpler but still sufficient for calculations without incurring a loss of accuracy for essential analysis.
Improved Structural Analysis
Incorporating the Nastran solution 146 monpnt1 rms supplements the Time-based RMS approach, which provides several advantages in obtaining dynamic response over time. While it takes the mean of the changing values, it offers a better way to analyze structures’ behaviour based on the load changes. This is most apparent in dynamic aeroelasticity, where varying aerodynamic loads cause dramatic shifts in structure response. RMS values’ employment proves useful because, when used to evaluate design, it enhances performance and safety alongside reliability.
Key to Dynamic Analysis
Productivity in the simulations and short cycles in the design process. The systematic methodology of analysis of dynamic behaviour through the RMS approach is used effectively in the aerospace industry, where reliability and integrity of flight structure are highly desirable features. Therefore, the Monpnt1 RMS technique is an important element of the dynamic aeroelastic analysis and design toolset.
Practical Applications and Examples
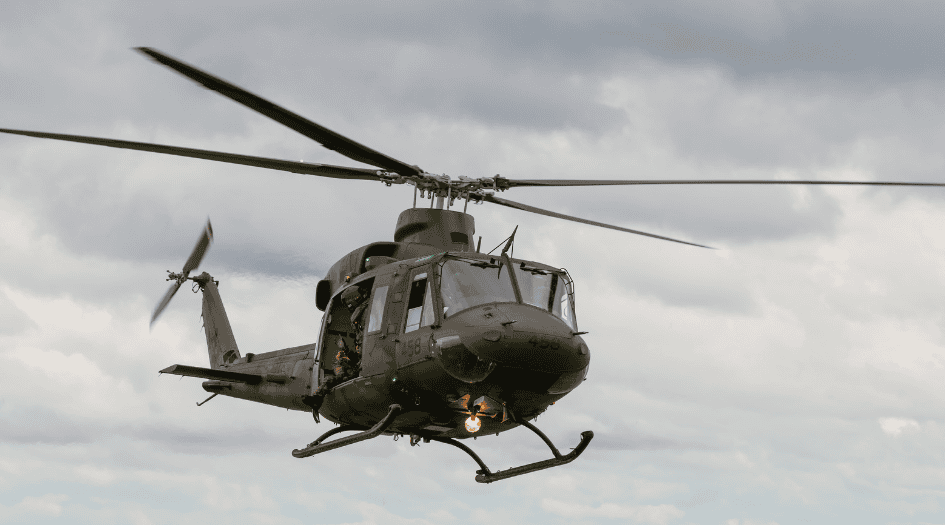
Optimizing Structural Performance
The Nastran Solution 146 Monpnt1 RMS methodology has been used in many engineering disciplines, especially in dynamic analysis such as aeroelasticity. One well-known example of its application is in the aerospace industry, where researchers employ this solution to investigate the deformation of planes’ wings during staking. A study done by an aerospace manufacturer saw the Nastran solution being used for wing optimization. The aim here was to reduce overall structure mass while at the same time guaranteeing that wings are strong enough to withstand the forces of turbulent flying. Through this dynamic analysis, the engineers were able to pinpoint areas of stress concentration and recommend design changes that would improve the performance and safety of the structures.
Real-World Impact
Likewise, in wind energy, Nastran Solution 146 Monpnt1 RMS plays a great role in analyzing the dynamics of the wind turbine blade. In one case, engineers encountered difficulties in analyzing the stiffness and strength of turbine configurations subjected to different wind loads. By applying this solution, they were able to approximate other actual conditions and gain deeper knowledge as to how blades would behave under dynamic interference. The result of such an approach was a much more efficient blade design that offered longer functional characteristics and lower operations prices, proving the realistic application value of this analysis.
Applications in Automotive
Apart from the airline and renewable energy industries, other industries like automobiles also utilize the Nastran solution for similar applications. For example, a major automobile manufacturer measures aerodynamic loads on structures in high-velocity tests. The use of the Nastran solution gave insights into the improvement of vehicle performance and the enhancement of passenger safety. These examples demonstrate how the Nastran Solution 146 Monpnt1 RMS has been applied across many different engineering fields and how it plays an active part in providing answers and challenging design and analysis methods.
Conclusion
Nastran Solution 146 Monpnt1 RMS makes this particular area dynamic aeroelasticity one of the versatile tools in identifying dynamic loading scenarios. It is crucial for engineers who often analyze the behaviour of structures under dynamic loads, and throughout this guide, key features and results of this solution are discussed. Nastran analysis gives detailed information that leads to the ability to understand the interactions between them as the vital factor in the safety and performance of various aerospace applications.
Thus, the stakeholders, especially in aerospace engineering and related disciplines, should gain a better insight into using Nastran Solution 146 Monpnt1 RMS for dynamic aeroelasticity purposes. If implemented into its workflow, this knowledge will ultimately lead to enhanced results in understanding dynamic load characteristics.